Comprehending What is Porosity in Welding: Causes and Solutions
Comprehending What is Porosity in Welding: Causes and Solutions
Blog Article
Porosity in Welding: Identifying Common Issues and Implementing Finest Practices for Prevention
Porosity in welding is a pervasive concern that commonly goes unnoticed until it creates significant problems with the stability of welds. This usual flaw can jeopardize the toughness and toughness of welded structures, posturing safety dangers and bring about expensive rework. By understanding the origin creates of porosity and applying reliable avoidance approaches, welders can substantially boost the quality and integrity of their welds. In this conversation, we will discover the essential variables adding to porosity development, analyze its detrimental results on weld performance, and talk about the best methods that can be embraced to decrease porosity occurrence in welding processes.
Typical Root Causes Of Porosity
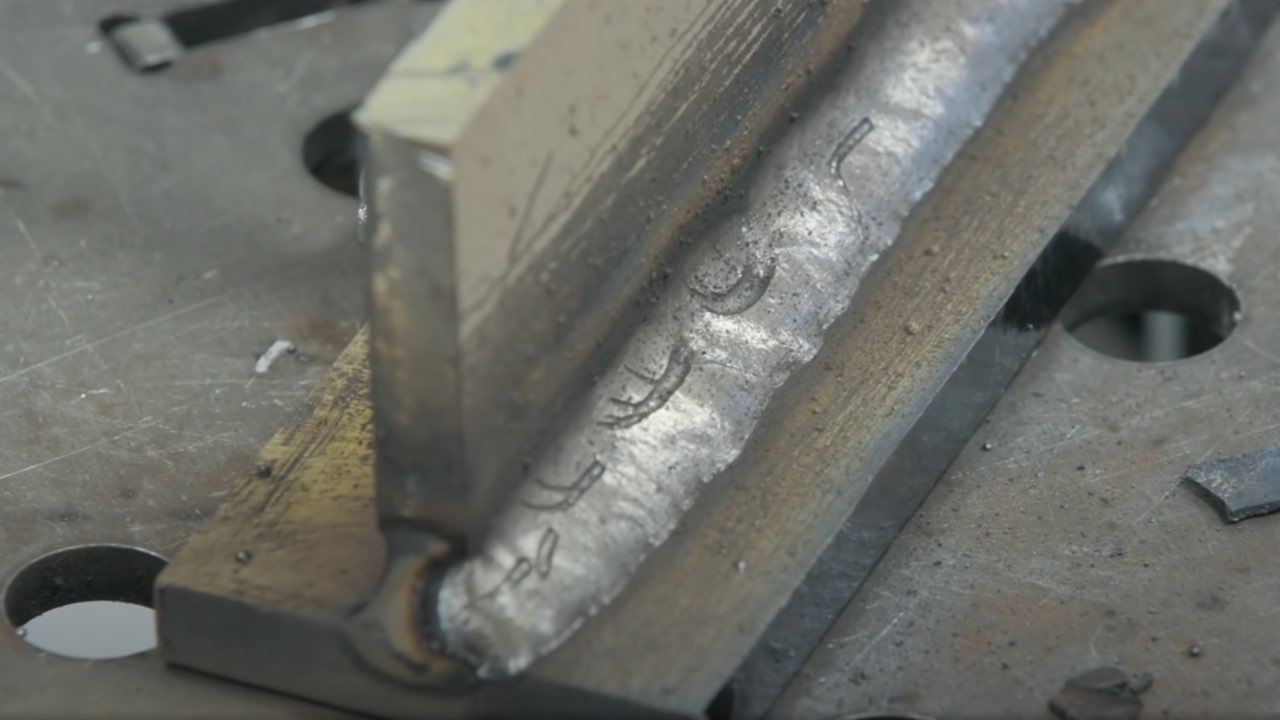
Another regular offender behind porosity is the presence of impurities externally of the base metal, such as oil, grease, or corrosion. When these pollutants are not efficiently gotten rid of prior to welding, they can evaporate and come to be trapped in the weld, triggering flaws. Using filthy or damp filler products can present pollutants into the weld, adding to porosity concerns. To minimize these usual reasons of porosity, detailed cleansing of base metals, correct securing gas choice, and adherence to optimal welding criteria are crucial methods in achieving high-quality, porosity-free welds.
Influence of Porosity on Weld Quality

The visibility of porosity in welding can substantially compromise the architectural integrity and mechanical homes of bonded joints. Porosity creates spaces within the weld metal, compromising its total strength and load-bearing capability. These gaps serve as stress and anxiety concentration factors, making the weld more at risk to fracturing and failure under used loads. Furthermore, porosity can lower the weld's resistance to rust and other ecological variables, additionally lessening its durability and efficiency.
One of the main effects of porosity is a decline in the weld's ductility and toughness. Welds with high porosity levels tend to display lower effect stamina and minimized capability to warp plastically prior to fracturing. This can be specifically worrying in applications where the bonded parts undergo vibrant or cyclic loading problems. Furthermore, porosity can impede the weld's ability to efficiently transmit forces, resulting in premature weld failure and potential safety hazards in crucial structures.
Finest Practices for Porosity Prevention
To boost the structural integrity and top quality of bonded joints, what particular measures can be carried out to reduce the occurrence of porosity throughout the welding process? Porosity avoidance in welding is important to ensure the honesty and stamina of the final weld. One reliable practice is proper cleansing of the base metal, getting rid of any type of contaminants such as rust, oil, paint, or dampness that might lead to read this post here gas entrapment. Making certain that the welding equipment remains in good problem, with clean consumables and proper gas circulation rates, can additionally considerably lower porosity. Furthermore, keeping a stable arc and managing the welding parameters, such as voltage, present, and travel rate, helps produce a regular weld pool that decreases the danger of gas entrapment. Making use of the correct welding method for the details material being welded, such as changing the welding angle and weapon position, can additionally protect against porosity. Regular assessment of welds and prompt remediation of any type of problems recognized throughout the welding process are crucial techniques to prevent porosity and produce high-grade welds.
Significance of Appropriate Welding Methods
Applying proper welding techniques is vital in ensuring the structural integrity and high quality of bonded joints, developing upon the foundation of reliable porosity avoidance actions. Welding strategies directly influence the general stamina and sturdiness of the bonded structure. One essential aspect of proper welding methods is maintaining the correct warmth input. Too much warm can lead to increased porosity as a result of the entrapment of gases in the weld swimming pool. On the other hand, insufficient heat might lead to insufficient combination, creating possible powerlessness in the joint. Additionally, utilizing the ideal welding criteria, such as voltage, this hyperlink current, and take a trip speed, is essential for attaining sound welds with marginal porosity.
Moreover, the selection of welding process, whether it be MIG, TIG, or stick welding, must straighten with the particular demands of the task to ensure ideal outcomes. Proper cleansing and preparation of the base steel, along with selecting the best filler product, are additionally important elements of skillful welding techniques. By adhering to these finest methods, welders can decrease the risk of porosity development and produce premium, structurally audio welds.

Checking and Quality Assurance Measures
Quality control procedures play an essential function in validating the honesty and reliability of welded joints. Evaluating treatments are vital to spot and avoid porosity in welding, making sure the toughness and durability of the final product. Non-destructive testing methods such as ultrasonic testing, radiographic testing, and why not try here visual evaluation are typically utilized to identify prospective flaws like porosity. These methods permit the evaluation of weld high quality without jeopardizing the stability of the joint. What is Porosity.
Post-weld examinations, on the other hand, evaluate the last weld for any kind of problems, consisting of porosity, and validate that it meets specified criteria. Implementing an extensive top quality control strategy that consists of comprehensive screening treatments and inspections is vital to lowering porosity concerns and ensuring the general high quality of bonded joints.
Verdict
In verdict, porosity in welding can be a common issue that impacts the high quality of welds. By determining the usual reasons for porosity and applying ideal practices for prevention, such as proper welding methods and testing actions, welders can make certain high top quality and dependable welds. It is vital to focus on avoidance approaches to decrease the event of porosity and maintain the integrity of bonded frameworks.
Report this page